Public and private: a successful marriage in the construction industry
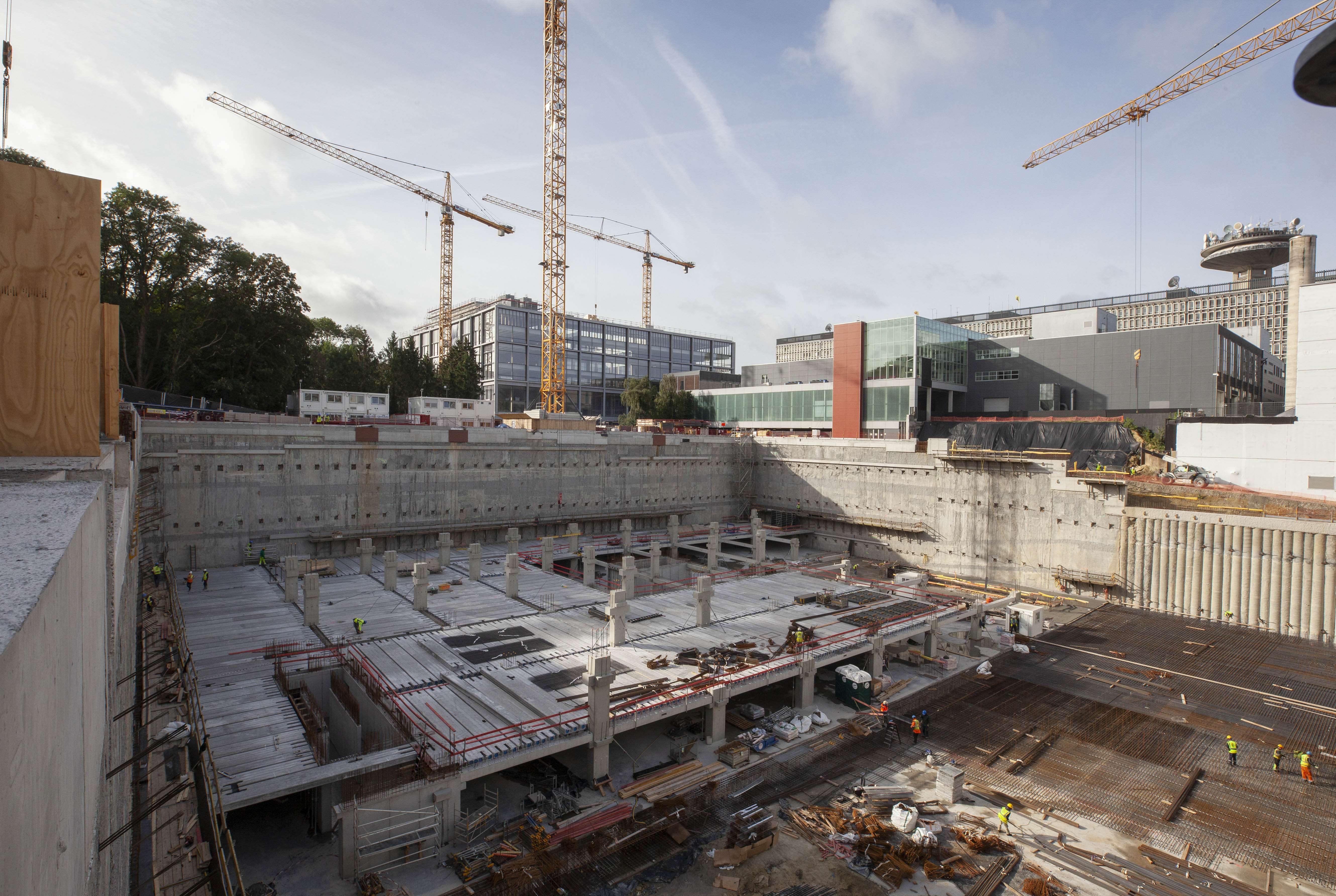
Double interview with Kristien De Vries, PPP Manager and Thomas Tassignon, Project Leader Civil Works
Wanted: helicopter view
What is the difference between public-private partnerships (PPPs) and conventional contracts?
Thomas Tassignon: “In a conventional contract, you simply execute what the client designs and follow a set of imposed specifica tions. In PPP projects, the contractor designs itself, according to pre-established high-level requirements. An example: cars must be able to get from point A to B via a bridge over road X. Or: the building must house 400 prisoners. You then set to work with these objectives in mind.
Also, at the design stage, you already strongly consider the maintenance of your construction which you usually must do for yourself. If, as a contractor, you also provide the financing, your periodic fee is even linked to that maintenance. You only get paid if your building or infrastructure is available and meets the quality requirements.”
Kristien De Vries: “The actual operation can also be part of the contractor’s assignments. Think of security, cleaning or landscaping services. In short, in a conventional project, Build (B) is the only focus. In PPP projects, Design (D) is added, and in many cases so are Finance (F), Maintain (M) and Operate (O).
"In PPP projects, you start with a blank sheet and must write down the whole story yourself, and that is exactly our strength."
Kristien De Vries, PPP Manager
Why are PPP projects on the rise in recent years?
Kristien: “Unburdening. For instance, prison managers want to focus on the correct execution of sentences and on preparing detainees for their return to society. Other matters are not part of their core business. Complex construction projects, for instance, they prefer to leave to others. And, if possible, by way of one contract covering the entire life cycle of a project.”
Thomas: “In that sense, it is also about risk allocation. In PPP projects, a private consortium takes the lead and the risks lie with the parties that can best manage those risks. There is a lot to be said for that. Furthermore, the client can expect a timely delivery and assured quality.”
Jan De Nul Group serves a unique cocktail
Why is Jan De Nul Group the ideal partner for PPP projects?
Kristien: The combined expertise of our various departments is a huge asset. I am talking here about both our technical departments – from remediation to ecosystems – and non-technical departments – from finance to legal. For each PPP project, we put together a multidisciplinary team. People from all over the organisation are involved.”
Thomas: “We started our first DBFM infra structure project back in 2011 and our first DBFM buildings project in 2014. So you can say that by now we have acquired plenty of experience. Add to that our solid financial strength and the critical mindset of an engineering company, and you get a unique cocktail.
How does that critical mindset translate into practice?
Thomas: “We do not shy away from questioning things. For instance, in a project, how can we work even more sustainably using certain materials or technologies? We are at our best when we can actively steer a project. We will certainly rise to any challenge.”
“We are at our best when we can actively steer a project.”
Thomas Tassignon, Project Leader Civil Works
Do these PPP projects also involve risks?
Kristien: Definitely. I am thinking mainly of the cost of competing for winning a project. As the scope is so extensive, we work on it with quite a few people. Also, a contract is only finally awarded as soon as all the necessary permits have been obtained. Apart from the preliminary process, every project phase – design, construc tion, pre-financing, maintenance, operation – comes with its own risks.”
Thomas: “The integrated approach to PPP projects requires broader competences from our people. But there is also an advantage in that. This makes each PPP project a unique learning experience for our employees. The accumulated expertise comes in handy again for the next project. This is how we stay on top of all challenges and trends.”
Prison in Antwerp
Design, Build, Finance, Maintain, Operate
This walled town comprises 7 buildings where more than 400 detainees will live. Executed almost entirely in prefab to guarantee a short construction period.
VRT building
Design, Build, Maintain
The new 65,000 m² building at the Reyerslaan will optimally integrate the landscape and exude flexibility. Accessibility label A++ is the goal.
Air bases in Florennes and Kleine Brogel and Defence Headquarters
Design, Build, Maintain
Two air bases for the F-35 fighter aircraft and a new headquarters in Brussels for the Belgian military. In the high-security buildings, 4,000 employees will manage all military operations. The project is also utterly sustainable, including a BEO field, solar panels and heat pumps.
Traffic hub R0xA201
Design, Build, Finance, Maintain
The new intersection of the Brussels Ring road with the A201 will be the first Single Point Interchange in Belgium. Amongst other things, we are building 12 bridges and 4 tunnels, and re-uncovering the Woluwe waterway. Keywords are safety, liveability, accessibility and nature development.